Whats is Concrete?
Concrete is a construction material obtained by mixing cement, fine aggregate (sand) coarse aggregates (gravel, stone chips, rock, etc), and water in certain proportions. All these ingredients when properly mixed, cement, and water start a reaction to bind themselves producing a plastic mass that hardens over time. This plastic and hardened mass is known as concrete.
The properties of concrete depend upon the quantity and proportions of the ingredients used in the mix. However, the properties can also be majorly modified based on the various type of cement used for the mix. Concrete is very strong in compression but little in tension. Fresh concrete can be poured into any suitable forms or moulds to get desired shape and size. Concrete is widely used in all types of construction work like building, bridges, dams, roads, flyovers, etc.
Composition of Concrete
1. Binding Materials: The use of lime in concrete has gone. Today cement is the only binding material used in concrete. When water is added with all the concrete ingredients a reaction between cement and water takes place and concrete is formed.
2. Aggregates: Aggregates are used as filer materials. They do not undergo any chemical change, they only provide mass volume to the concrete and reduce shrinkage effects.
3. Water: Water is required to complete the chemical reaction with cement. Water plays a vital role in workability of concrete.
4. Admixtures: Admixture is an optional material added during concrete mixing to enhance the properties and performance of fresh concrete. Their are 4 types of admixture- Accelerating admixture, Retarding admixture, Air entraining admixture, and Water reducing admixture.
Types of Concrete
1. Plain Cement Concrete (PCC):
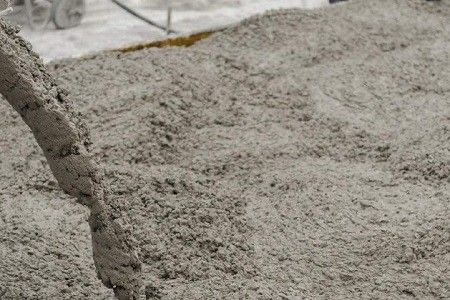
Plain Cement Concrete is a basic concrete mix consisting of cement. fine aggregates, coarse aggregates, admixtures (optional), and water. PCC is very strong in compression. But, due to the absence of reinforcements like steel, it is very weak in tension. The general mix design ratio of PCC is 1:2:4 and 1:3:6. It is commonly used in the foundation of a building. After the hard strata have been reached, a layer of sand is laid followed by Plain Cement Concrete. Above the Plain cement concrete, the reinforcement cage of the footing is placed.
Applications:
- Foundations
- Grade slabs
- Concrete blocks
- Verandas
- Open Parking
2. Reinforced Cement Concrete (RCC)
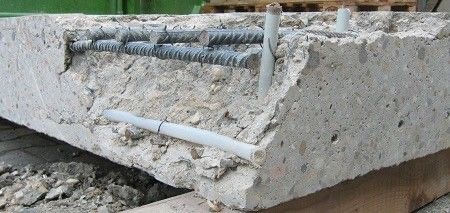
Reinforced cement concrete is a composite material made up of cement, fine aggregates, coarse aggregates, admixtures, and steel reinforcements. It is simply Plain cement concrete with the presence of steel in it. All the limitations in Plain cement concrete can be overcome by reinforced cement concrete. Of all metals, steel is the most suitable reinforcement material because of the near same thermal coefficient of expansion. The thermal coefficient of concrete is 14.5 /C and that of steel is 12 /°C. Due to this property of steel, it is more compatible with concrete than other metals.
Applications:
- Slabs, beams, columns & foundations of buildings
- Dams, Pavements, Bridges Water tanks, Retaining walls
- Underwater constructions, Concrete sewers & pipes Canals
- Chimneys, Power plants
3.Fibre Reinforced Concrete (FRC):
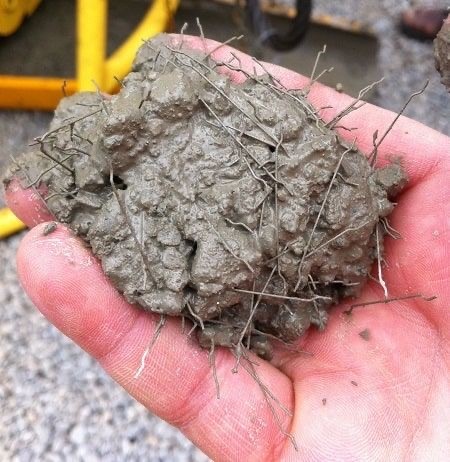
Fibre reinforced concrete is a composite material made up of cement, water, aggregates, and flat or rounded fibres. Various types of fibres like steel fibres, polypropylene fibres, glass fibres, asbestos fibres, carbon fibres and organic fibres are widely used to reduce permeability, bleeding and the formation of minor cracks. Fibres are added in the ratio of 0.1% to 3% of the total volume of the concrete. The dimensions of the fibres are represented using the term “aspect ratio” which is the ratio of the length to the diameter of the fibre. The aspect ratio of the fibre is generally 30 to 150. The orientation of the fibres is mostly random but they can be arranged in parallel or perpendicular fashion depending on the design criteria.
Applications:
- Dams, spillways, basins
- Pavements in airports and highways
- Bridge decks, Thin shelled structures
- Foundation, In refractories, Industrial floors, Machine foundation
4.Ready Mix Concrete
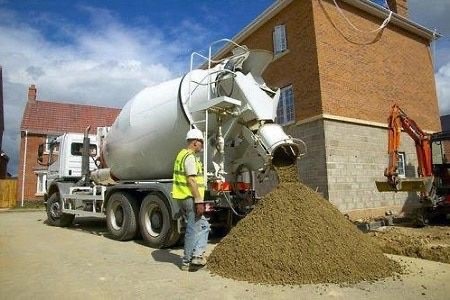
Ready mix concrete is a factory-made concrete made of cement, aggregates, water, and admixtures and transported to the site. The ready-mix concrete is preferred when there is less space for storing and mixing the construction materials. The plant-made concrete is loaded into special delivery trucks called the transit mixers which have the provisions to constantly rotate and keep the concrete in motion and prevent setting.
Usually, retarders are added to the concrete mix to slow down the setting process to give allowance to the transportation and placing the time of the concrete. Quality check is performed both in the factory and at the site.
The difference in the slump value of both should not differ by more than 25 mm or 1/8th of the specific value whichever is greater.
Applications:
- Normally used for monolithic concreting of the roof slabs and beams
- Runways
- Pavements
- Lining of tunnels
- Dams and hydraulic structures
5. Precast Concrete
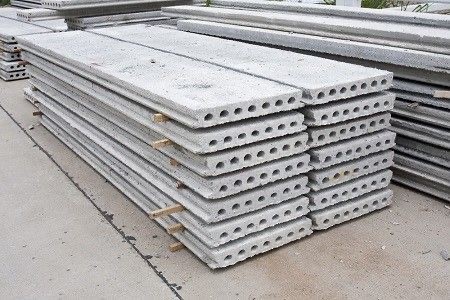
Precast concrete structures are cast, cured, transported to the site, and erected using cranes. The precast structures are manufactured at the sites using moulds with reinforcement cages present inside them. They may or may not be prestressed based on requirements. The dried concrete members are cured in controlled conditions to achieve the desired strength. Special hooks are provided to the members to lift them. The design of precast members takes into account the handling and erection stresses that may arise during the construction process.
Applications:
- Precast slabs, beams, columns, wall panels can be used for conventional buildings
- Bridge decks, Parking, High rise building, Retaining walls, Sound walls, Culverts
6. Prestressed Concrete
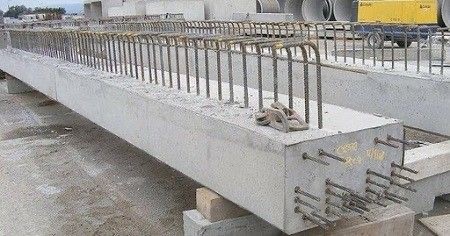
Prestressed concrete structures are made up of high-strength concrete and high-strength steel tendons in addition to the normal reinforcements. When the tendons are prestressed, the stress from the tendon is transferred to the concrete. Thus it improves the deflection resistance, load capacity, and overall structural performance of the member. Prestressed concrete structures are commonly used in the construction of prefabricated buildings.
A concrete member can be prestressed in two ways:
- Pre-tensioning
- Post-tensioning
Read more +
Pretensioned prestressed structures are prestressed before the concrete hardens. First, the high strength tendons are pulled and the concrete is cast in the mould with the normal reinforcement and the pulled tendons. After the concrete has sufficiently hardened, the prestressing tendons are spliced and the stress is transferred to the member. Here the stress transfer is through the bond strength between the concrete and steel. This is called pre-tensioning.
In Post tensioned prestressed structures, the concrete member is the first cast with the conventional reinforcement and special ducts. After hardening, high strength steelare introduced into the ducts and are prestressed and anchored to the ends of the member. Here the stress transfer is through the bond strength and anchorage blocks of the members This is called post- tensioning. The post-tensioned slabs are mostly precast and are of various shapes. Post-tensioned slabs are widely used because of their ability to be cast in a shorter period of time.
Applications:
- Bridge decks
- Parking
- High rise buildings
- Retaining walls
- Sound walls
- Culverts
7. Light Weight Concrete
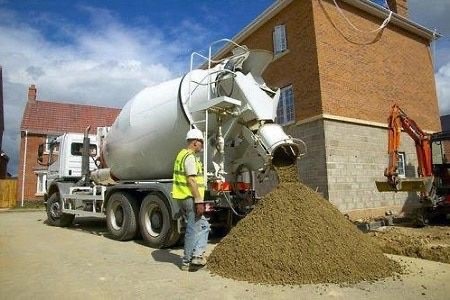
Light weight concrete is a special type of concrete used to reduce the self- weight of the structure. The reduction in self-weight can be achieved by any weight of the structure. The reduction in self-weight can be achieved by any of the following methods
1. Light Weight Aggregate Concrete:
Using light weight aggregates like silica sand, pumice, sawdust, scoria, volcanic cinder blocks, volcanic slag, tuff, crushed stone, and synthetic aggregates like coke breeze, foamed slag, bloated clay, expanded perlite, thermocol beads, broken bricks etc.
2. Aerated Concrete:
The concrete can be made light by increasing the air density inside to concrete from 300 kg/cu.m to 800 kg/cu.m. The air can be introduced by chemical reactions, using foam or chemicals like aluminum powder, hydrogen peroxide, and zinc compounds.
3. No fines Concrete:
In this concrete, the self-weight is reduced by removing the fine aggregates in the concrete. No fines concrete is made up of cement, coarse aggregate, and water. The Aggregate to cement ratio is set between 6:1 and 10:1.
Application:
- In precast elements
- Bridge decks
- Long span structures
- Filling for floor and roof slabs
- Partition walls
8. High Density Concrete
High-density concrete is a special type of concrete made up of cement, water fine aggregate, coarse aggregate, and high-density aggregate. The density of normal Plain cement concrete is 2400 kg/m3. For high- density concrete, the density ranges from 3360 kg/m3 to 3840 kg/m3. The density of the concrete is increased by increasing the cement content, reducing voids, and using high-density aggregates like barite, magnetite, serpentine, limonite, goethite, etc.,
Applications:
- Power plants
- Coal plants
- Research institutes
9. High Performance Concrete
High-performance concrete is a special type of concrete made using cement, water, fine aggregate, coarse aggregate, mineral admixtures, and superplasticizers.
The mix design ratio of the high-performance concrete is designed in such a way that it performs well both structurally and in durability criteria. The performance of the concrete can be improved by making the three phases of the concrete – the paste phase, transition phase, and aggregate phase stronger.
It can be done by increasing the cement content, restricting the water- cement ratio to not more than 0.3, using superplasticizers, mineral admixtures, and non-porous aggregates.
Applications:
- Power plants
- Chemical industries
- Coal plant
- Research Institutes
10. High Strength Concrete
High strength concrete is a special type of concrete that is made up of cement, water, fine aggregate, coarse aggregate, mineral admixtures, and superplasticizers. Mineral admixtures like fly ash, ground granulated blast furnace slaq, silica fume, rice husk ash have a high specific surface area which plays a major role in increasing the strength. High-strength concrete has a compressive strength of at least 70 MPa.
High-strength concrete is used in the precast industry. The concrete has to be strong enough to withstand the huge amount of prestressing that will be transferred through the process.
11. Self-compacting Concrete (SCC)
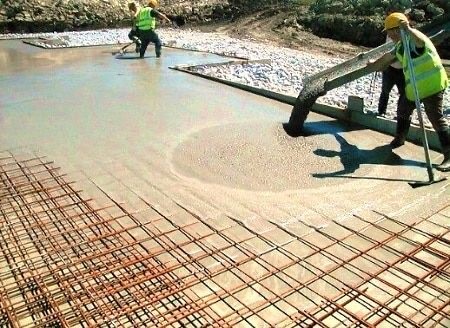
Self-compacting concrete is a special type of concrete made up of cement, fine aggregates, coarse aggregates, chemical admixtures to improve the work ability, flow ability, rheology, and mineral admixtures. SCC is also known as zero slump concrete. It has high work ability and does not require any extra compaction. It is used in congested reinforcements where it is quite complicated to achieve full compaction.
The flowability of the concrete can be achieved using viscosity modifying agents like sikaplast, retarders, air- entraining agents, very fine mineral admixtures, and superplasticizers.
Applications:
- In congested reinforcements like beam-column junctions.
- In places of heavy reinforcements.
- Places where compaction is not possible.
- Deep beams
12. Pumped Concrete
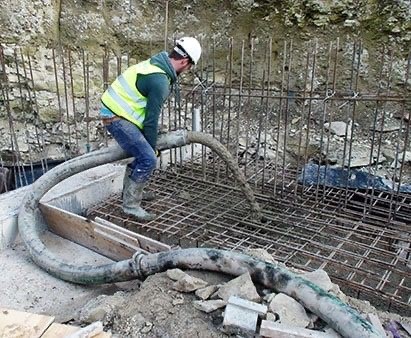
Pumped concrete is a special type of concrete that is suitable for pumping. Admixtures are added to improve the workability, flowability, and pumpability of the concrete.
Applications:
- Tall buildings
- Tunnels
- Underwater construction
13. DLC
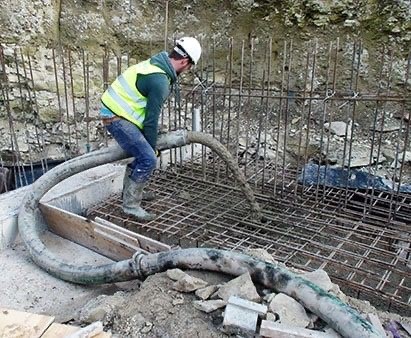
Dry Lean Concrete (DLC) is an important part of modern rigid pavement. It is a plain concrete with a large ratio of aggregate to cement than conventional concrete and generally used as a base/sub base of rigid pavement.
Type: Domestic & Commercial
14. PQC
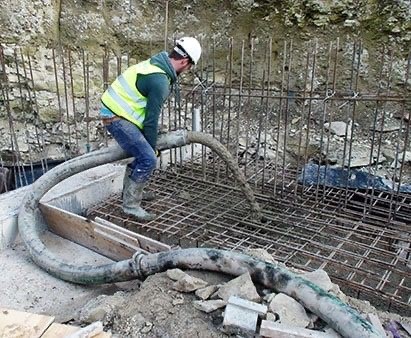
Pavement Quality Concrete (PQC) is normally employed for providing a strong surface of rigid pavements. PQC is also used for construction of runways in airports in order to distribute the heavy impact load from wheel to sub- grade layers.